Most DC motors are designed to utilize magnetic force. They contain many internal mechanisms, some electronic and some electromechanical. A feature of conventional DC motors is the commutator, whose function is to alternate the direction of the current. Brushless DC motors represent an improved form of the traditional DC motor, with more power, no sliding contacts and longer service life. In particular, the speed and torque of brushless motors can be precisely controlled over a wide range, which is why they are widely used in industry.
The basis for making a drone is a brushless motor. The combination of motor and propeller is necessary to keep the whole drone hovering in the air. For the drone to fly as long as possible, a balance needs to be found between the motor, the propeller and the weight of the entire structure. Like all electric motors, brushless motors contain bearings, coils, magnets, and stator and end caps connected by bearings. The important parameters of a brushless motor are KV value, weight, no-load current, the maximum current that can be carried and maximum voltage.
Brush motors are designed with brushes and phase changers to obtain a fixed direction of magnetic field force to rotate. Brushless motors do not have brushes and phase changers, so how do they obtain a fixed direction of magnetic field force? Simply put, by changing the alternating frequency and waveform of the current wave input to the stator coil of a brushless motor, a magnetic field is formed around the winding coil that rotates around the geometric axis of the motor, and this magnetic field drives the permanent magnets on the rotor to rotate, and the motor turns.
The diagram below depicts a typical operating cycle of a three-phase brushless motor. To turn the motor, an ESC is used to allow three phases of DC power to alternate. Each phase changes the switching state sequentially with time.
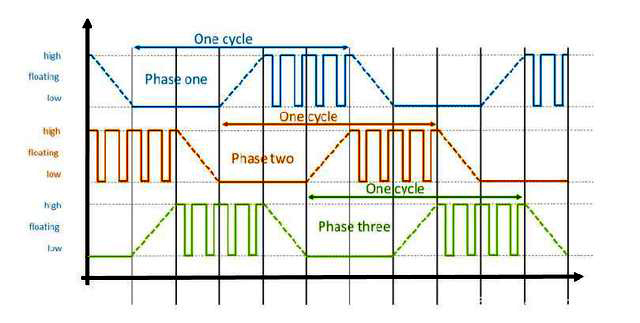
Why do most drones use brushless motors?
These motors have less friction and lower losses than brushed motors. Compared with brushed motors, brushless motors generate less heat, have a longer life, lower noise, run more smoothly, and have lower maintenance costs.
One of the most important parameters of a brushless motor is KV value, which is a performance parameter unique to the brushless motor and is important data to judge the performance characteristics of a brushless motor. Brushless drone motors with 100~1500KV are provided on Brushless.com.
- The KV value of the brushless motor is defined as RPM/volts, meaning that the input voltage increases by 1 volt, and the RPM value of the brushless motor idling speed increases.
- From the first point, we can know that brushless motor voltage input and motor idling speed follow a strict linear proportional relationship.
- For example, the KV value of the brushless motor is 100KV, which means that this motor has a speed of 100 revolutions per minute at 1V. Then at 10V, the speed of this motor is 10V * 100KV = 1000 rpm, of course, these are in the motor no-load time.
- The same motor, winding more turns, KV value is low, the highest output current is small, but the torque is large, and the motor shape is flat and thick.
- In the same motor, the winding turns less, KV value is high, the highest output current is large, but the torque is small, and the motor shape is thin and high.
These are the reasons why drones use brushless motors. People who want to know more about brushless drone motors can leave us a message, and we will have the corresponding answer.