350W brushless dc electric motor for car, wide speed range, rated torque 1.12Nm, maximum torque 3.35Nm, speed at 3000rpm, 36V industrial brushless motor is suitable for applications requiring torque from low to high speed.
Basic Specifications
Model: SKU: BLDC-D5BLD350
Matched Controller Model: BLD-750
Rated Power: 350W
Rated Voltage: 36V
Rated Current: 12.19A
Phase: 3 phase
Rated Torque: 1.12 Nm
Max. Torque: 3.35 Nm
Rated Speed: 3000 rpm for standard (or 2000 rpm when matching the worm gearbox)
No-load Speed: 3300 rpm
No-load Current: <8.4A
Square Flange Size: 86 mm
Working Efficiency: 85%
Insulation Grade: F
Protection Grade: IP54
Motor Lead Length: 1 meter
Certificate: CE, RoHS, ISO
Weight: 6 kg
Note: Power, Voltage, Speed, Shaft, Motor Length, and Motor Lead of BLDC Motors can be customized.
Features
- Stable speed control: 36V brushless motor continues to set speed and a feedback signal is compared from the speed of the motor to adjust the voltage applied to the motor; therefore, even if the load change, still can set the speed from slow instantaneous adjustment to, and in order to stabilize the running speed.
- Thin, high power: 3 phase DC motor adopts a permanent magnet brushless motor rotor, thus realizing the thin and high power.
- Wide speed control range: 350W brushless DC motor speed control range than speed ac motor and inverter wider, because unlike the speed ac motor that at low speed have restrictions on the use of torque, so there is no brush motor is suitable for from low speed to high speed, all require the use of a certain torque.
- Contribute to energy saving: The rotor of the brushless dc electric motor is used for the permanent magnet, which can reduce the two-loss of the rotor, so the power consumption is reduced by more than 20% compared with the three-phase induction motor with variable frequency control, which is helpful for the energy saving of the device.
- Equipped with protection function: 36V 350W BLDC motor can help to protect the safety of the equipment system.
Dimension (Unit: mm)
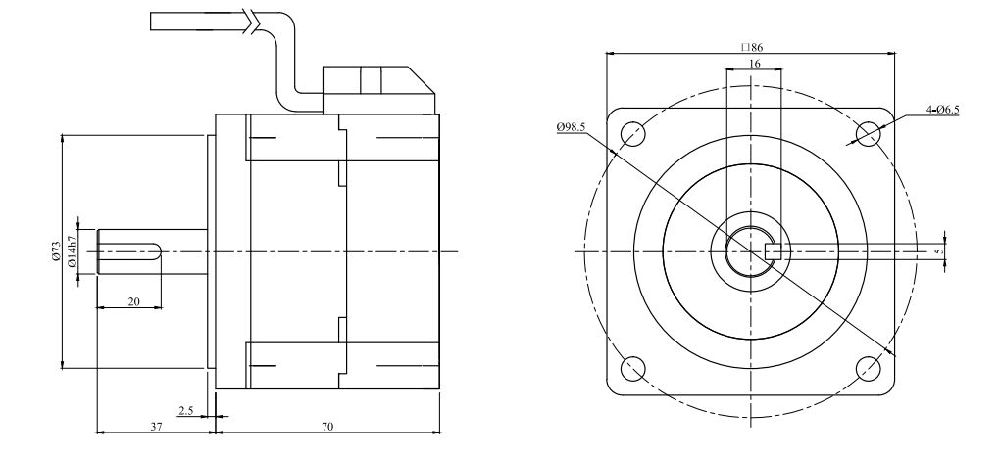
Speed - Torque Curve

- Instantaneous maximum torque line
The maximum torque momentarily impacts the load when the motor is started.
Beyond this torque, the over-current protection of the driver will cause the motor to stop.
- Short-time operation area
The motor can run for a short time within this torque range at different speeds.
If the operation time is too long, the motor will generate heat, which may cause the motor to stop or burn.
- Rated operating torque line
The rated torque of the motor runs at different speeds, and the motor can run for a long time at this torque.
- Continuous operating area
When the motor rotates at different speeds, it runs continuously in this corresponding zone.
Line Define
Power Wire |
Hall Wire |
Red |
U |
Red |
5V |
Yellow |
V |
Black |
GND |
Black |
W |
Hu |
Blue |
Hv |
Green |
Hw |
White |
Details
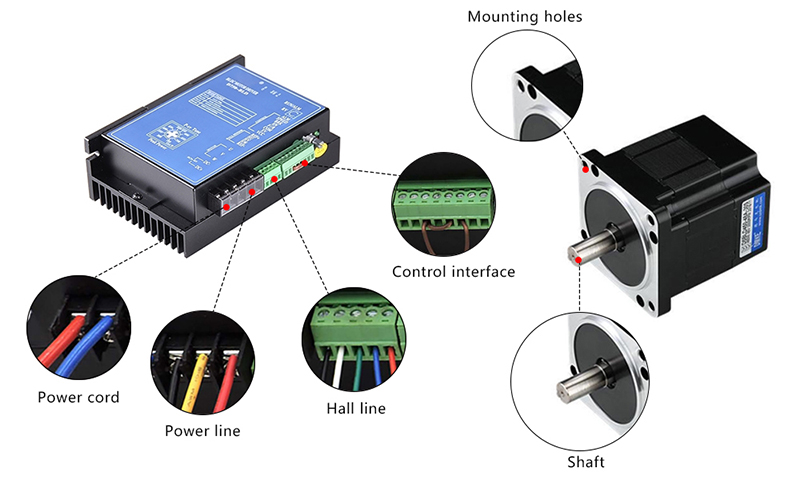
Applications
Brushless DC motors are widely used in our lives, such as electric bicycles, inverter air conditioners, washing machines, drones, automobiles, CNC machine tools, polishing and grinding equipment, packaging machinery, tools, turnstiles, industrial control, medical machinery, automation to, AGV trolley, aerospace and intelligent storage equipment, etc.
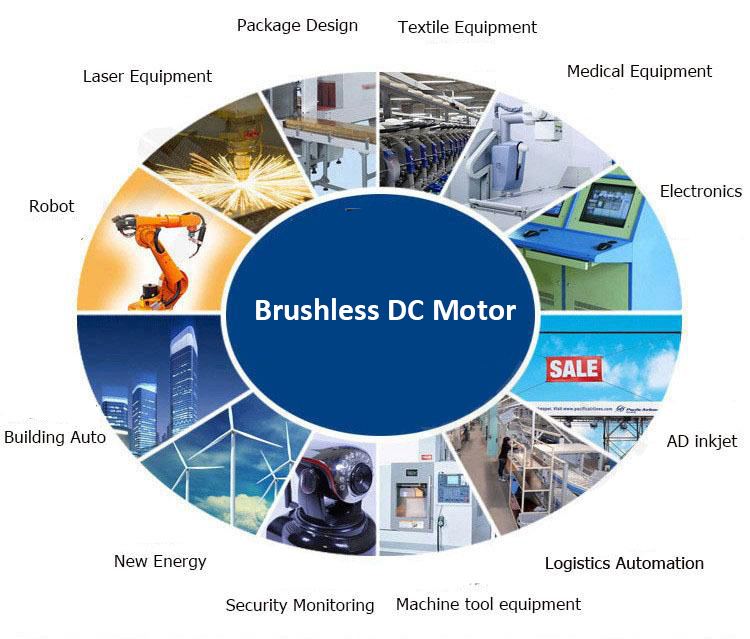
Tips: What is the displacement of the hall sensor for a 350W brushless DC motor?
The 350W brushless DC motor is a Hall sensor with 120-degree displacement. In fact, the correct position of the position sensor is also related to the following factors: the characteristics of the sensor itself, polarity regulations, the structure of the stator and rotor of the main motor, the structure of the stator winding (such as phase band, coil winding direction, how much short distance, double layer or single layer, etc.), the relative position of the rotor of the main motor and the rotor of the sensor, and the logic design of the controller, so it must be agreed first. The method proposed here is able to resolve the above complications and determine the correct position of the Hall position sensor in a relatively simple way.