This 250-watt frameless brushless DC motor features a rated torque of 1.77 Nm, making it perfectly suited for tasks requiring stable and precise rotational force. Choose this 36V frameless brushless DC motor to elevate your project with unparalleled reliability, precision, and efficiency.
Specifications
- Model: BLDC-WK6010
- Rated Power: 266.4W
- Nominal Voltage: 36V
- Nominal Current: 7.4A
- Nominal Torque: 1.77 Nm
- Nominal Speed: 504 rpm
- Max Speed: 720 rpm
- Stall Torque: 2.68 Nm
- Stall Current: 10.67A
- Winding Turs of Motor: 30T
- Phase to Phase Resistance: 3.5Ω
- Phase to Phase Inductance: 10.07Mh
- Speed Constant: 20 rpm/V
- Torque Constant: 0.23 Nm/A
- Rotor Inertia: 1645 gcm2
- Number of Pole Pairs: 14
- Motor Weight: 345g
- Working Temperature: -20~80℃
- Max Demagnetize Temperature: 120℃
Features
- The frameless configuration allows seamless integration into applications, saving space and offering greater flexibility in custom designs.
- This frameless brushless DC motor with a rotational speed of 504 rpm, is ideal for applications requiring precise control and smooth operation at lower speeds.
- The frameless BLDC motor delivers a power output of 250W while operating at 36V, ensuring energy-efficient performance with minimal heat generation.
- Brushless design minimizes maintenance, reduces wear and tear, and enhances durability for prolonged operational life.
- Its frameless construction and low-speed operation make it perfect for direct-drive setups, eliminating the need for additional gearing mechanisms.
- Frameless brushless motors offer the flexibility to design and customize your motor housing, making them ideal for DIY and tailored engineering projects.
Dimensions (Unit: mm)

Applications
Frameless Brushless DC Motors are designed for seamless integration into systems where space, weight, and precision are critical. Due to their high efficiency, compact design, and reliability, these motors are commonly used in robotics, drones, medical devices, and industrial automation.
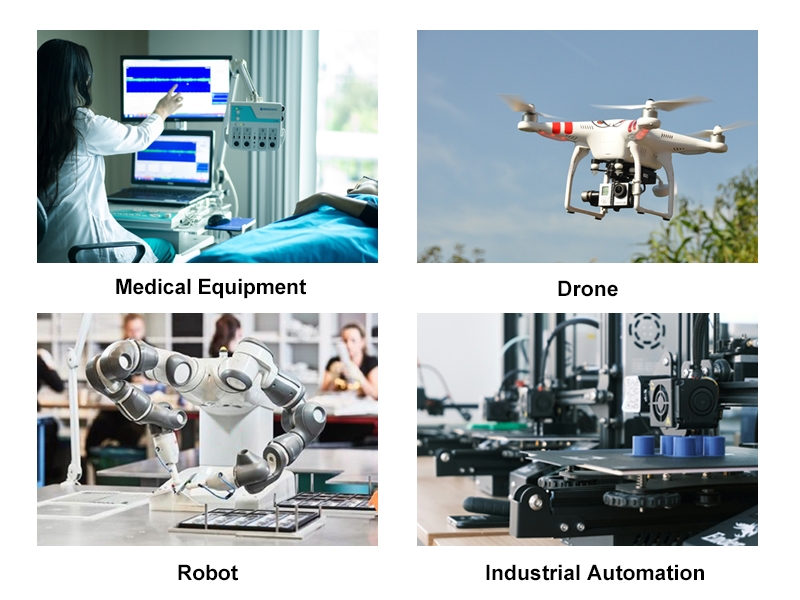
Tips: What controllers are compatible with frameless BLDC motors?
- Sensorless Controllers: Use back-EMF to detect rotor position, suitable for cost-effective applications but with limited low-speed control.
- Sensor-based Controllers: Use position sensors (like Hall sensors or encoders) for precise control, ideal for high-precision needs.
- FOC Controllers: Field-Oriented Control (FOC) optimizes performance, providing smoother operation and higher efficiency.
- PWM Controllers: Use Pulse Width Modulation to control speed and torque, commonly in simpler applications.
- Integrated Controllers: Combine the motor and controller in one unit for easy integration.