Reliable 200W brushless dc gear motor, rated current 20.83A at 12V, 10.42A at 24V, 5.21A at 48V, peak torque 1.91 Nm, gear reduction motor is made of high quality segmental steel, steel cast iron case, gear surface with high frequency heat treatment, with the advantages of low vibration, low noise and high energy saving.
Basic Specifications
Model |
BLDC-D5BLD200-12 |
BLDC-D5BLD200-24 |
BLDC-D5BLD200-48 |
Voltage |
12V |
24V |
48V |
Rated Current |
20.83A |
10.42A |
5.21A |
No-load Current |
< 6.2A |
< 4.13A |
< 1.61A |
Compatible Driver Model |
BLD-KVD2412N |
BLD-300B |
Power |
200W |
Rated Speed |
3000 rpm |
No-load Speed |
3300 rpm |
Rated Torque |
0.64 N.m |
Peak Torque |
1.91 N.m |
Weight |
3 kg |
Protection Grade |
IP54 |
Motor Lead Length |
300mm |
Temperature |
0~50℃ |
Gearbox Model |
2GN□K Enter the gear ratio into the box (□) within the model name |
Gear Ratio |
3, 5, 7.5, 10, 12.5, 15, 18, 20, 25, 30, 36, 40, 50, 60, 75, 90, 100, 120, 150, 180, 200 |
The allowable torque with a gearbox
Gear Ratio |
Speed (r/min) |
Allowable Torque (N.m) |
Allowable Torque (kgf.cm) |
3 |
1000 |
1.55 |
15.47 |
5 |
600 |
2.58 |
25.79 |
7.5 |
400 |
3.87 |
38.68 |
10 |
300 |
5.16 |
51.57 |
12.5 |
240 |
5.81 |
58.1 |
15 |
200 |
6.97 |
69.72 |
18 |
167 |
8.37 |
83.66 |
20 |
150 |
8.4 |
84.04 |
25 |
120 |
10.51 |
105.1 |
30 |
100 |
12.61 |
126.1 |
36 |
83.33 |
15.13 |
151.3 |
40 |
75 |
16.81 |
168.1 |
50 |
60 |
20 |
200 |
60 |
50 |
20 |
200 |
75 |
40 |
20 |
200 |
90 |
33 |
20 |
200 |
100 |
30 |
20 |
200 |
120 |
25 |
20 |
200 |
150 |
20 |
20 |
200 |
180 |
17 |
20 |
200 |
200 |
15 |
20 |
200 |
Line Define
Power Wire |
Hall Wire |
Red |
U |
Red |
5V |
Yellow |
V |
Black |
GND |
Black |
W |
Hu |
Blue |
Hv |
Green |
Hw |
White |
DC Gear Motor Dimension (Unit=mm)
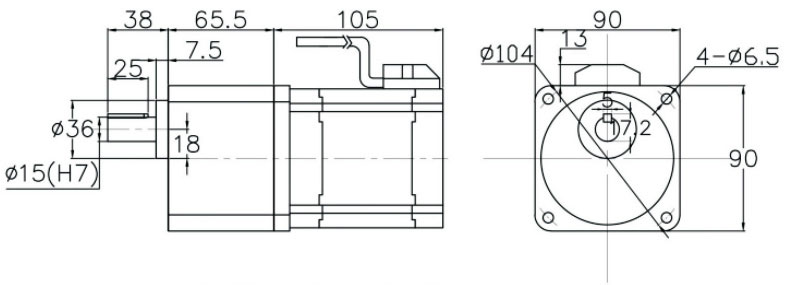
Applications
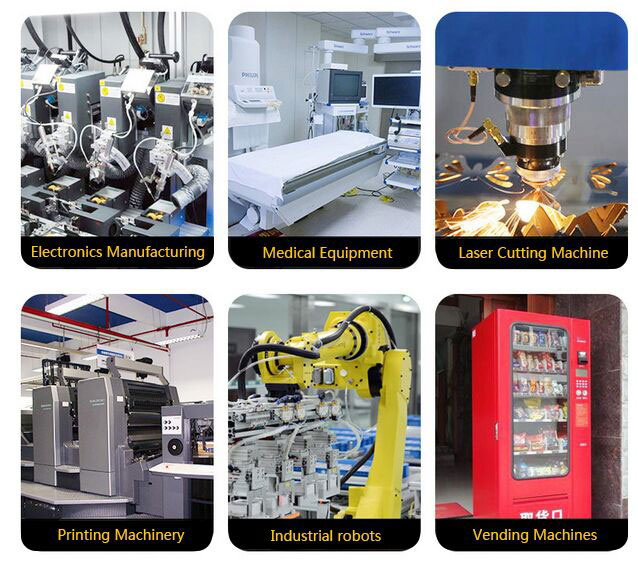
Tips: How to use a 12V brushless DC gear motor?
When using a 12V gear motor (including reversible gear motors), it is important to consider the running and starting torque separately, as gearing and starting characteristics may vary. The most important factors when confirming torque include the amount of work that can be done by the gear motor and its speed and considering the use of AC motors for optimal function.
When using a geared motor with a brake, the low inertia rotor of a fully integrated geared motor will match the characteristics of the gearbox and provide controlled load reduction. AC motors also enable point-to-point positioning applications and indexing of geared motors with encoders to understand the motor type. When you know the type of motor being used, you can improve its efficiency by replacing the PMC motor with a PSC motor.